Rapid Prototyping vs. Traditional Methods: What Chicago Manufacturers Need to Know
Understanding Rapid Prototyping
In the ever-evolving landscape of manufacturing, rapid prototyping has emerged as a game-changer, particularly for manufacturers in bustling hubs like Chicago. This innovative approach leverages advanced technologies to create a scale model of a physical part or assembly using three-dimensional computer-aided design (CAD) data. The process is swift and efficient, allowing for quick iterations and improvements. But how does it stack up against traditional methods?
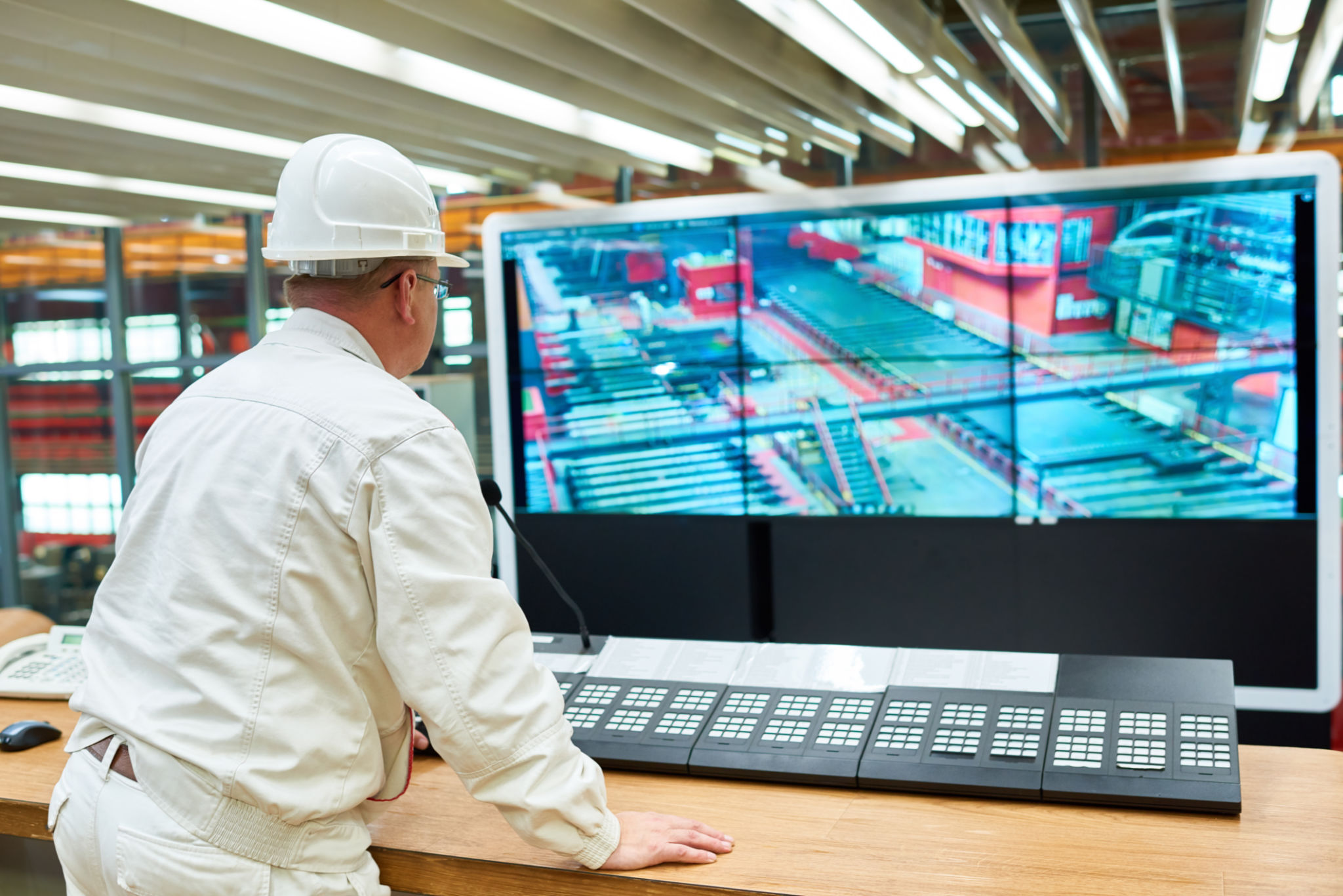
Speed and Flexibility
One of the most significant advantages of rapid prototyping is its speed. Unlike traditional manufacturing methods, which can take weeks or even months to develop a prototype, rapid prototyping can produce a model in a matter of days. This speed allows manufacturers to test and refine their designs quickly, ensuring a faster time-to-market for new products. Additionally, the flexibility of rapid prototyping means that changes can be made easily, without the need for costly and time-consuming tooling modifications.
Traditional Manufacturing Methods
Traditional manufacturing methods, such as CNC machining and injection molding, have been the backbone of the industry for decades. These methods are well-established and offer high precision and durability. However, they often require significant upfront investment in tooling and setup, making them less attractive for projects that require frequent design changes or small production runs.
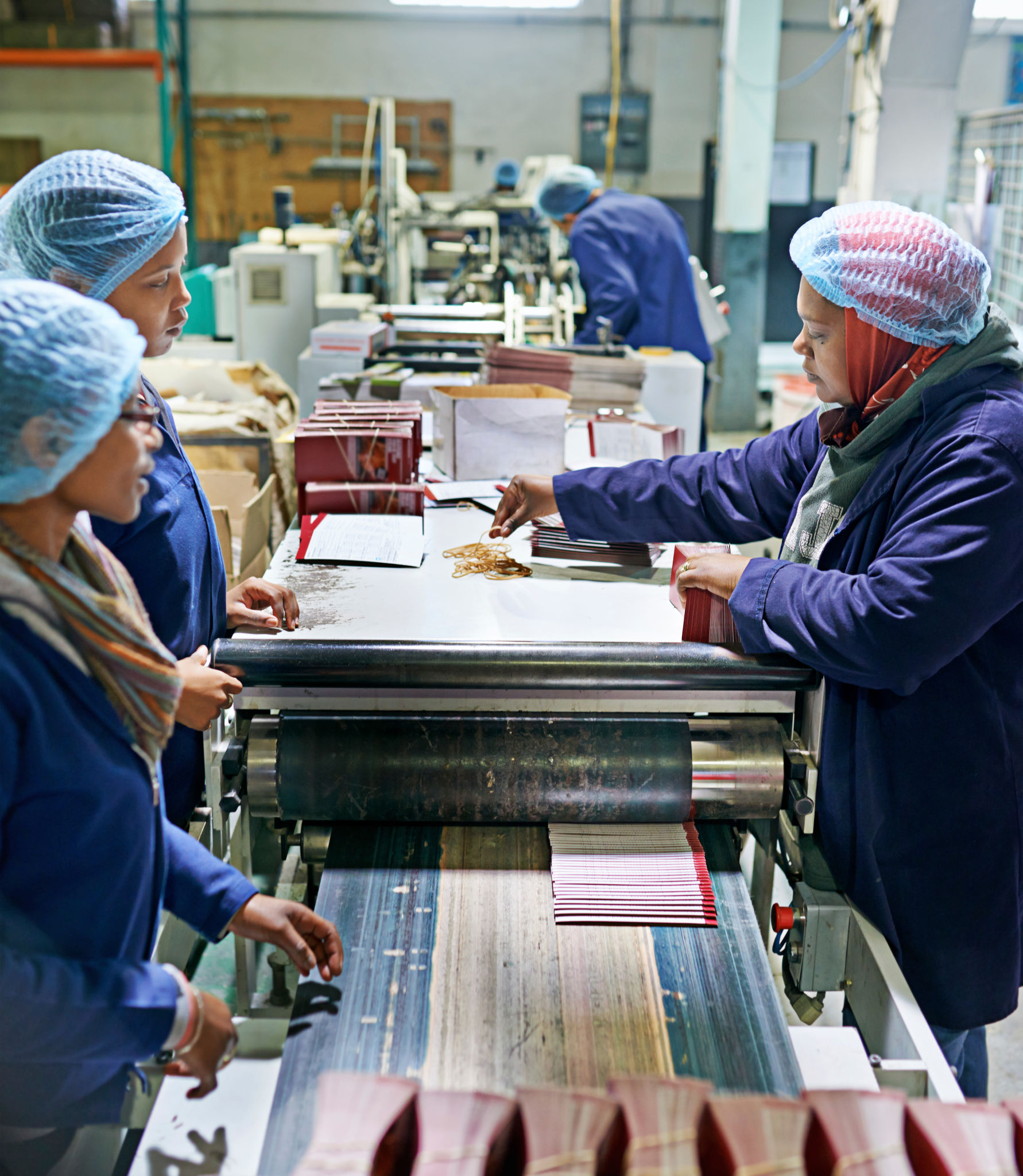
Cost Considerations
When it comes to cost, both rapid prototyping and traditional methods have their pros and cons. Rapid prototyping can be more cost-effective for small batches and complex designs due to the reduced need for expensive tooling. On the other hand, traditional methods may offer cost advantages for large-scale production where the initial investment can be amortized over a high volume of units. Chicago manufacturers need to carefully evaluate their production needs and budget constraints to determine the best approach.
Material and Design Flexibility
Rapid prototyping offers unparalleled material and design flexibility. With the advent of 3D printing technologies, manufacturers can experiment with a wide range of materials, from plastics to metals, and create intricate designs that would be difficult or impossible to achieve with traditional methods. This flexibility is particularly beneficial for industries that require custom or complex parts, such as aerospace and medical devices.
Quality and Precision
While rapid prototyping is excellent for testing and development, traditional methods still hold the upper hand when it comes to the quality and precision of the final product. Processes like CNC machining provide a high level of accuracy and finish, which is crucial for applications where the slightest deviation can lead to significant issues. Manufacturers must weigh the importance of precision against the need for speed and flexibility in their projects.
Choosing the Right Method
For Chicago manufacturers, the decision between rapid prototyping and traditional methods depends on several factors, including the complexity of the design, production volume, budget, and timeline. A hybrid approach, leveraging the strengths of both methods, can often provide the best results. By using rapid prototyping for initial design validation and traditional methods for final production, manufacturers can optimize both cost and quality.
Ultimately, the choice between rapid prototyping and traditional manufacturing methods is not a one-size-fits-all decision. By understanding the strengths and limitations of each approach, manufacturers can make informed decisions that align with their specific project requirements and business goals.